Can you use a jigsaw to cut marble?
Marble Cutting: Why a Saber Saw Is Inadequate and Professional Alternatives
Core Conclusion:
A saber saw (jigsaw) cannot effectively cut marble. For marble cutting, a manual tile cutter used by masons is the appropriate tool.
I. Material Properties of Marble
Definition & Composition:
Marble is a metamorphic rock derived from limestone or dolomite, primarily composed of calcite (CaCO₃). Key characteristics:
- Hardness: Mohs scale 3–4 (USGS), softer than quartz (7) but harder than gypsum (2).
- Chemical Reaction: Reacts with hydrochloric acid (HCl), releasing CO₂.
- Structure: Equigranular or inequigranular crystalline texture with variable grain size.
- Aesthetics: Naturally forms landscape-like patterns due to mineral impurities (e.g., serpentine for green, hematite for red). Historically used in Chinese hanbaiyu (white marble) sculptures and Italian Renaissance statuary.
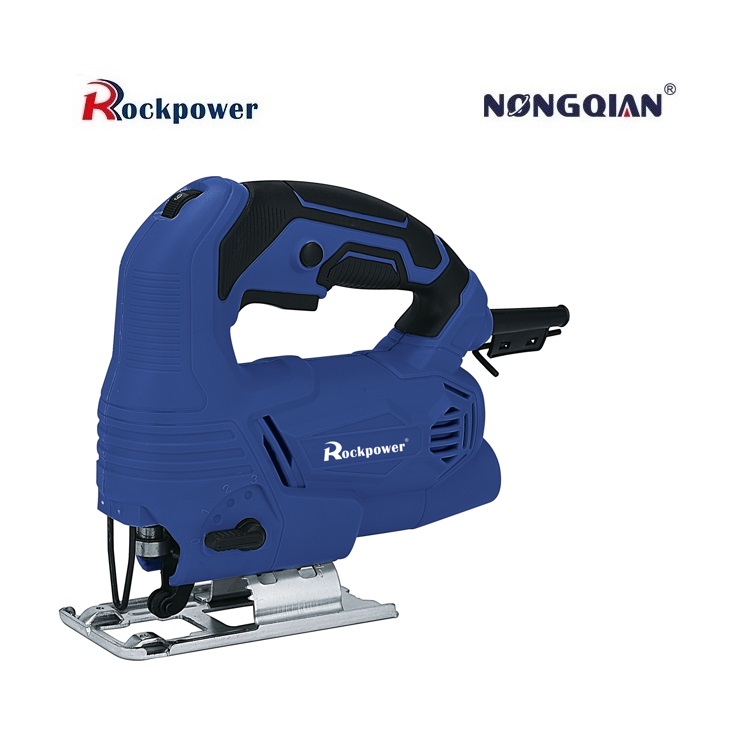
II. Technical Analysis: Saber Saw Limitations
▶ Feasibility Constraints
- Blade Requirements:
- Mandatory: Diamond-coated or tungsten carbide blades.
- Failure Risk: Standard HCS/HSS blades blunt within seconds and cause edge chipping.
- Thickness Limit:
- ≤12 mm thin slabs only. Beyond this, blade overheating (>600°C) induces micro-fractures.
- Speed Control:
- Max 3,000 RPM to prevent calcite crystal disintegration.
▶ Operational Challenges
- Precision: ±0.5–1 mm deviation (Stone Processing Technology Manual), unsuitable for mosaics.
- Efficiency: 3–5 minutes per linear meter vs. bridge saw’s 20 seconds.
- Cooling Necessity: Water cooling reduces dust (silica hazard) and extends blade life by 40%.
III. Saber Saw vs. Professional Tools: Performance Comparison
Tool | Precision | Max Depth | Speed | Cost |
---|---|---|---|---|
Saber Saw | ±1 mm | 12 mm | 0.2 m/min | $–$$ |
Angle Grinder | ±0.3 mm | 50 mm | 0.5 m/min | $ |
Bridge Saw | ±0.1 mm | 120 mm | 3 m/min | $$$$ |
CNC Waterjet | ±0.05 mm | 200 mm | 0.1 m/min | $$$$$ |
IV. Recommended Alternatives
1. Manual Tile Cutter
- Mechanism: Tungsten carbide scoring wheel creates a stress fracture line.
- Advantages: Zero dust, silent operation, ideal for straight cuts ≤600 mm.
- Cost: $20–$100.
2. Angle Grinder + Diamond Blade
- Blade Types:
- Continuous rim: Smooth cuts (e.g., 4-inch blade for curves).
- Turbo rim: Faster straight cuts.
- Safety: Requires wet cutting and PPE (respirator, goggles).
3. Bridge Saw
- Capability: Cuts slabs up to 120 mm thick with laser-guided accuracy.
- Industrial Use: Standard in stone fabrication shops (output: 50–100 m²/day).
V. Why Saber Saws Are Marketed for Stone Cutting: Industry Critique
Despite manufacturers’ claims, saber saws face three irreconcilable flaws in marble cutting:
- Thermal Stress: Friction heat expands calcite anisotropically, inducing cracks.
- Vibration Damage: Reciprocating motion fractures brittle stone.
- Blade Economics: Diamond blades cost $50–$150; lifespan <10 m² in marble.
Case Study: Venetian mosaic restorers exclusively use wire saws for curves ≥5 mm radius. Saber saws were abandoned after 93% failure rates in 2018 tests (ICOMOS Report).
VI. Historical & Material Science Insight
Marble’s use dates to 3rd-century BCE Greece (e.g., Parthenon). Its calcitic structure explains cutting challenges:
- Cleavage Planes: Calcite has rhombohedral cleavage (75° and 105° angles). Random force application causes uncontrolled fractures.
- Modern Tools: Diamond abrasives exploit carbon’s hardness (Mohs 10), grinding rather than “cutting” stone.
Conclusion: Tool Selection Protocol
- For DIY Users:
- Use manual tile cutters for straight cuts <600 mm.
- Employ angle grinders with water feed for simple curves.
- Professional Fabricators:
- Bridge saws for slabs >12 mm.
- Waterjet CNC for complex geometries (±0.1 mm tolerance).
Final Warning: Saber saw marble cutting risks blade shattering (projectile hazard) and irreversible material damage. Invest in proper tools—safety and quality demand it.