Can you cut marble with water?
Can You Cut Marble with Water? Absolutely! Not only can water cut marble, it does so with incredible precision and quality, making it a top choice for high-end stonework.
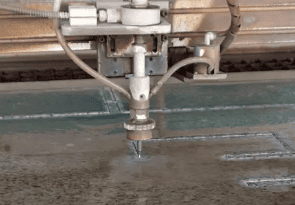
How Does a Waterjet Cutter Work?
At its core, a waterjet cutter is a tool that harnesses the power of ultra-high-pressure water. Here’s how it works:
- Pressurization: A powerful pump forces water through a tiny diamond or sapphire nozzle at pressures ranging from 50,000 to 90,000 PSI (significantly higher than the 5,000-8,000 PSI mentioned earlier – that range is too low for effective cutting, especially stone).
- Abrasive Addition (For Hard Materials): For cutting hard substances like marble, granite, or metal, garnet sand (a very hard mineral) is precisely mixed into the ultra-high-pressure water stream just before it exits the cutting head. This transforms the pure waterjet into an abrasive slurry jet.
- Cutting Action: This supersonic stream of water and abrasive particles (traveling over 3 times the speed of sound) hits the material with immense kinetic energy. The abrasive particles do the majority of the cutting work by eroding tiny particles of the material away along a very narrow path. The water acts as the carrier and accelerator for the abrasive and helps flush away the debris.
- Computer Control: The cutting head is mounted on a computer-controlled (CNC) gantry system. This allows it to move with extreme precision along any programmed path, enabling it to cut intricate shapes, curves, and internal cuts (by drilling a starter hole first).
Simplified diagram of abrasive waterjet cutting process
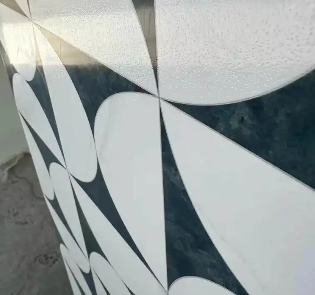
Can a Waterjet Specifically Cut Marble?
Yes, abrasive waterjet cutting is exceptionally well-suited for cutting marble. While marble is a hard natural stone, it is also relatively brittle and sensitive to heat. Traditional methods like diamond saws or grinders generate significant heat and mechanical stress, increasing the risk of chipping, cracking, or thermal damage (like discoloration).
The abrasive waterjet excels here because it is a cold cutting process. The high-speed water and abrasive particles remove material through erosion, generating minimal heat at the cut zone. This prevents thermal stress, cracking, and changes to the marble’s color or crystalline structure. Furthermore, the waterjet produces very little mechanical force or vibration on the workpiece, drastically reducing the chance of breakage, especially near edges or on thin sections.
Advantages of Waterjet Cutting for Marble
- Cold Cutting (No Heat Damage)
This is paramount for marble. Unlike laser, plasma, or even high-friction diamond cutting, the waterjet generates negligible heat. This eliminates:- Thermal Cracking: Sudden temperature changes won’t cause micro-fractures that weaken the stone or become visible later.
- Discoloration/Burning: The natural color and veining of the marble remain pristine. No unsightly brown burn marks or yellowing.
- Structural Integrity: The crystalline structure of the marble isn’t altered by heat stress.
- Exceptional Edge Quality & Precision
Waterjets produce remarkably clean and smooth cuts in marble:- Minimal Chipping/Breakout: The controlled erosion process significantly reduces the risk of the brittle marble chipping along the cut edge, especially compared to saws.
- Smooth Finish: The cut edge often has a fine, honed-like finish, frequently requiring little to no secondary polishing for many applications, saving significant time and labor.
- Narrow Kerf: The cutting stream is very thin, typically around 1.0mm to 1.2mm when using abrasive. This wastes far less valuable marble compared to the wider kerf of diamond saw blades (which can be 5mm, 10mm, or even wider).
- High Accuracy & Repeatability: CNC control allows for cuts accurate to within 0.1mm – 0.25mm, perfect for intricate details and tight-fitting joints.
Close-up of a smooth marble edge cut by waterjet
- Unmatched Design Flexibility & Complexity Waterjets are not constrained by the limitations of rotating blades. They excel at cutting intricate shapes:
- Complex Curves & Profiles: Seamlessly cut graceful curves, waves, or custom sink outlines.
- Internal Cuts & Cutouts: Easily cut holes for sinks, faucets, cooktops, or decorative inserts without needing to start from an edge.
- Inlays & Mosaics: Achieve pinpoint accuracy for creating intricate tile mosaics, decorative borders, or precisely fitting stone inlays within other stone.
- 3D Contouring: Advanced systems can even perform controlled taper cuts or simple 3D shaping.
Intricate marble design cut using waterjet technology
- Reduced Dust and Health Hazard
Cutting dry generates large amounts of harmful crystalline silica dust, a known carcinogen causing silicosis. Waterjet cutting:- Substantially Suppresses Dust: The cutting process happens within a curtain of water, and the slurry captures most particles.
- Creates Slurry, Not Airborne Dust: The waste material is flushed away as a wet slurry, drastically improving workshop air quality and protecting operator health.
- Cleaner Work Environment: Less dust means cleaner machines and a generally tidier workspace.
- Material Savings
The narrow kerf (cut width) of the waterjet, as mentioned earlier, translates directly into less wasted material. For expensive natural stone like marble, this efficiency significantly reduces costs and allows for more pieces to be cut from a single slab. - Safety
Beyond dust suppression:- No Fire Hazard: Unlike thermal processes, there are no sparks or extreme heat.
- Reduced Fragmentation Risk: The minimal mechanical stress lowers the chance of the stone shattering unexpectedly during cutting.
Why is Waterjet Highly Recommended for Marble Countertops?
All the advantages above converge to make waterjet the premier choice for fabricating high-end marble countertops:
- Critical Sink & Cooktop Cutouts: Achieving perfectly smooth, unchipped edges on the fragile inside corners of sink cutouts or cooktop openings is extremely difficult with saws. Waterjets excel here.
- Complex Edge Profiles: Creating intricate ogee, dupont, or custom waterfall edges without breakage is far more reliable with a waterjet.
- Integrated Drainboards or Backsplashes: Seamlessly cutting complex shapes that integrate different functional parts of the countertop.
- Decorative Elements: Incorporating inlays, medallions, or intricate borders directly into the countertop surface.
- Minimized Material Waste: Maximizing yield from expensive marble slabs.
- Superior Final Appearance: The pristine, thermally undamaged surface and smooth cut edges require less finishing and look consistently high-quality.
Precise sink cutout in marble countertop using waterjet
What Else Can a Waterjet Cut?
Abrasive waterjets are astonishingly versatile “universal cutters.” They can cut virtually any material, with thicknesses ranging from paper-thin to over a foot thick in some metals:
- Metals: Steel (mild, hardened, tool, stainless), aluminum, copper, brass, titanium, inconel.
- Stone & Tile: Granite, marble, travertine, slate, porcelain, ceramic, glass (including laminated).
- Composites: Carbon fiber, fiberglass, Kevlar, laminates (like Formica, Corian).
- Plastics & Rubber: Acrylic, polycarbonate, PVC, neoprene, foam (with pure waterjet).
- Glass: Sheet glass, bulletproof glass, mirrors (edge quality can be an issue sometimes).
- Food: (Using pure waterjets) Frozen foods, cakes, pastries – hygienic and crumb-free.
- Specialized Materials: Textiles, gaskets, circuit boards, explosives (safely!), honeycomb structures.
The key advantages – no heat-affected zone, no mechanical stress, extreme versatility, high precision, and the ability to cut thick or layered materials – make waterjets indispensable in industries from aerospace and automotive to art, architecture, and manufacturing.
Conclusion
Not only can you cut marble with water, but abrasive waterjet cutting is often the best and most advanced method available for achieving high-quality, intricate results in this beautiful but demanding natural stone. Its cold-cutting nature preserves the marble’s integrity and aesthetics, its precision enables complex designs impossible with saws, and its efficiency minimizes waste and health hazards. While the equipment and operational expertise required represent a significant investment, the unparalleled quality, flexibility, and material savings make waterjet technology the gold standard for premium marble fabrication, especially for critical applications like countertops. From delicate artistic inlays to robust architectural elements, the waterjet unlocks the full potential of marble.